Once you decide to buy garbage sorting machines, do not rush to buy them. This is because choosing the best machines is difficult. Different companies, manufacturers, and online stores sell these machines. You need to be careful when looking for the best garbage sorting plant. Use biomass pelletizer to make fuel pellets from wood, sawdust, or other biomass.
Continue reading to learn how to choose the best sorting machines.
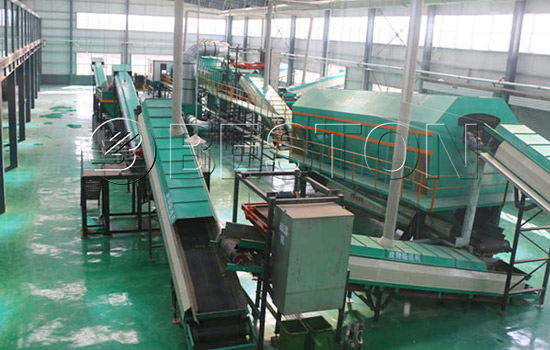
1. Read Customer Reviews
There are a lot of blogs and websites that have genuine customer reviews. These reviews can help you choose the right machine. To know about the quality, price, and maintenance of these machines, you need to read customer reviews. Then, choose a machine that has positive reviews.
However, some of these machines get a lot of negative reviews. Do not select them. Most of these machines will never last for a long time. You may end up spending a lot of money on the wrong machines. Make sure you are reading genuine reviews. Because some of these reviews are fake. When you find an efficient machine to recycle biomass waste, try apple tray machine.
2. Choose the Right Manufacturer of Garbage Sorting Machines
Choosing the right manufacturer can help you choose the right garbage sorting machine. It is easy to find the best manufacturers. They have been in this industry for a long time. They have a good reputation. They have excellent customer service. And they have the best machines in the market.
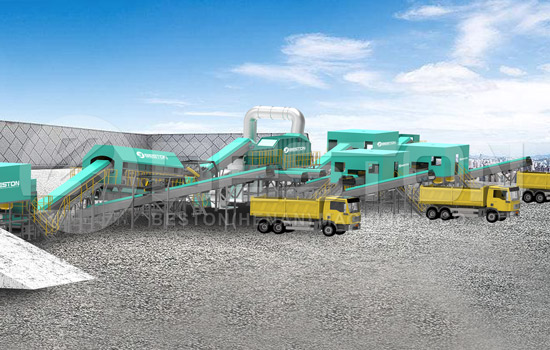
Once you find the best manufacturers in this industry, contact them. Ask them if they have sorting machines. If they do, they will tell you. And they will tell you the cost of their machines. Select a reputable manufacturer because it has the best machines in the market.
3. Tour Local Suppliers
Touring local suppliers can help you choose the best garbage sorting machines. Most suppliers have stayed in business for a long time because they work with reputable manufacturers. They get their machines from manufacturers that have a proven track record in this industry. Besides, the waste rubber pyrolysis plant can make oil from tyre, plastic and oil sludge.
If you select the right supplier, you will get the best machines from that supplier. However, some buyers do not even know how to select the right supplier. Talk to people who have used these suppliers. If you can find a reputable local supplier, you will find the best machines from that supplier.
4. The Price of the Garbage Sorting Machines
The prices of garbage sorting machines can determine the machine you will choose. There are both cheap and expensive machines on the market. However, most people assume the expensive machines are the best. Some of these machines are not that great.
To avoid spending a lot of money on the wrong machine, create a budget. A budget can help you choose the right machine. You will only compare machines that are within your price range. Therefore, it narrows down your decision. You will never have a problem choosing an affordable machine.
You now know how to choose the best garbage sorting machines. Choosing the right machine is not easy. Doing proper research helps. Or contact an experienced waste to energy plant manfuacturer. It is a good idea to buy this machine from this reputable manufacturer. Do not buy any machine from a seller you do not know or trust.